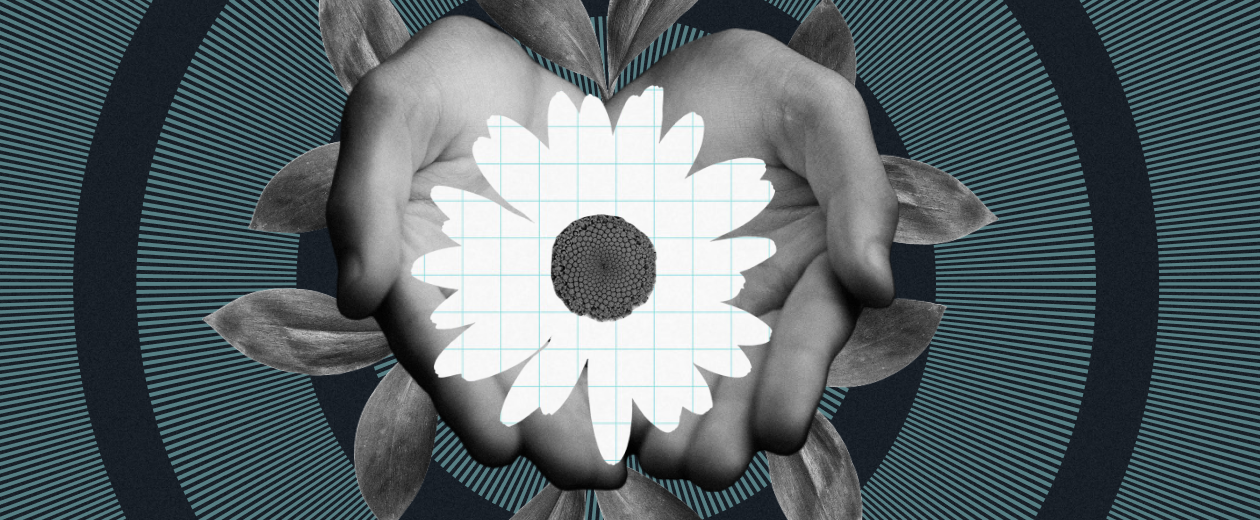
March 27, 2025
March 27, 2025
Reading time
July 10, 2024
October 21, 2022
Arshan Poursohi, CEO and cofounder of Third Wave Automation, discovered early on in his career an important life lesson he’s carried forward to guide his work in robotics, machine learning and industrial automation. He learned the value of accelerating the move of technologies out of the lab and into real-world environments.
“Talking to local operators early on to find out what they need better informs our technology so we can help them and solve their actual problems versus the theoretical problems we imagined in the lab,” Arshan said.
Prior to co-founding intelligent automation startup Third Wave Automation in 2018, which netted $40 million in Series B funding in August 2021, he worked at Sun Microsystems and Google. It was while at Sun Labs working on wireless sensor nodes that Arshan saw first-hand the gaps that often exist between lab thinking and real-world experience. In conversation with the U.S. Geological Survey, it became clear that in-the-field environmental work involved a very different set of parameters and challenges than he and his team had envisaged.
I recently chatted with Arshan about Third Wave’s concept of shared autonomy, the drivers behind the latest wave of automation and what’s coming next. What follows is an edited version of our conversation:
The three of us all had been working on robots at that point for some time. We were watching the technology curve get better and better and we’d built machines and proved they could do useful tasks. For instance, I was excited about my work at Toyota Research on eldercare robots for indoor environments. It turns out that you can do a lot of good to help people age in place with some very simple mechanisms—the robot doesn’t have to be an AI butler.
However, because of issues outside of my control, we weren’t able to ship the robots. This happened multiple times and it was frustrating. So, my co-founders and I started examining what we could do in robotics that could prove helpful and which we could ship within one to two years.
All of our backgrounds were in R&D so we had no shortage of ideas, everything from asteroid mining to underwater robots. The trick is finding a good idea. Forklifts rose to the top of our discussion. Once we decided we could develop the robotics, we then began examining the business case, and that's when we started talking to local operators in warehouses.
This idea of shared autonomy is the core of our technology. The concept is to have the forklift know whether or not it's safe to potentially do whatever it's planning to do. If it’s not safe, the machine stops and asks for help, and then learns from that experience and gets better in its responses.
What we address is that cliche of work that’s dull, dirty and dangerous. Instead of replacing the workforce, we’re augmenting them so they’re no longer sitting on a forklift where something heavy might fall on them. Instead, they can tell one or a fleet of forklifts what to do and also have the option of managing them remotely if needed.
To some degree, we're riding on the coattails of the on-road autonomous vehicle industry. The core research that they're engaged in makes it possible for us to do what we're doing. We use similar 3D digital Lidar sensors and compute platforms. Wireless technology is also becoming faster, more robust and a lot more reliable than it was 10 years ago.
The amazing thing about the technology curve the robotics industry has been on over the last decade is the move from engineering to data. You can gain examples of how to execute a task correctly or a predictive understanding of next actions.
<split-lines>"The amazing thing about the technology curve the robotics industry has been on over the last decade is the move from engineering to data."<split-lines>
You can change warehouse infrastructure, but you have to be careful about it. It's like swapping out the engine on a plane in mid-flight. If you automate one piece of operations without thinking about the neighboring sections, you might be shifting a heavy load to a person instead of making a better system overall. You need to make changes in the right order so the plane keeps flying while you change not only the engine, but the landing gear and how the cockpit functions.
With shared autonomy, we view our product as an integral part of the whole system. So, as we move our autonomous forklifts into a facility, we are then working with warehouse operators to make sure that their pallet throughput is always improving.
<split-lines>"You can change warehouse infrastructure, but you have to be careful about it. It's like swapping out the engine on a plane in mid-flight."<split-lines>
As far as I can tell, people are already trying to address every aspect of the supply chain and make it better with various forms of technology. The next step is integrating all of these up-and-coming, promising technologies together.
Today, we’re at an early stage. Conversations are taking place between companies like ourselves on how to bridge the integration points. For instance, there are many forms of automation that take pallets of goods and their movement as an input. So, being able to manage the workflow to provide the resources to that set of tasks makes sense.
It’s a lot like what the Internet of Things has gone through in the last five years or so, where it went from, ‘This thermostat is now IoT-ed, congratulations,’ to that device becoming part of a wider system that can sync with products from different companies. There were some failed attempts of different protocols which tried to bring all of these IoT systems into one ‘house,’ where you’d have control over it and the systems could work with each other.
It's much more important in a warehouse that these systems work together. For instance, we're participating in the MassRobotics Autonomous Mobile Robots (AMR) Interoperability Working Group. Together, the participants are collaborating on a protocol to share status information and machine location data so that we don’t cause deadlocks. We’re also working through integrations with existing warehouse execution systems.
<split-lines>"Get out of the lab sooner rather than later. When you have a hardware aspect to your product, you’ll find a lot of unexpected edge cases."<split-lines>
Get out of the lab sooner rather than later. When you have a hardware aspect to your product, you’ll find a lot of unexpected edge cases. The sooner you get your MVP (minimum viable product) out there, the sooner you’ll find those edge cases and start addressing them. For example, wood pallets splinter over time so warehouse floors are full of splinters as well as dust and water. By finding out how often an edge case occurs and how you deal with it, you can make sure that the worst case is still OK for your customers.
Another piece of advice I often give is that it's okay to work efficiently by finding the easier route. I think one mistake we made early on was wanting the robotics to really shine versus taking the path of least resistance. We did a lot of work that we didn’t necessarily need to do and which our customers didn’t require. By not doing the long pull first, we could have gotten our machines out into the real world sooner and started learning the lessons we could only discover once we deployed the forklifts.
So, find the shortcuts and take them. Don't be egotistical about it. Don't try to make a perfect machine because your product will always be ever-evolving. Get out there with your customers and learn. It’s not easy, but it equally won’t be easy for anyone to come in afterwards and try to replicate what you have already done.
March 10, 2025
March 10, 2025
February 21, 2025
February 20, 2025